Sodium Carboxy Methyl Cellulose(CMC)
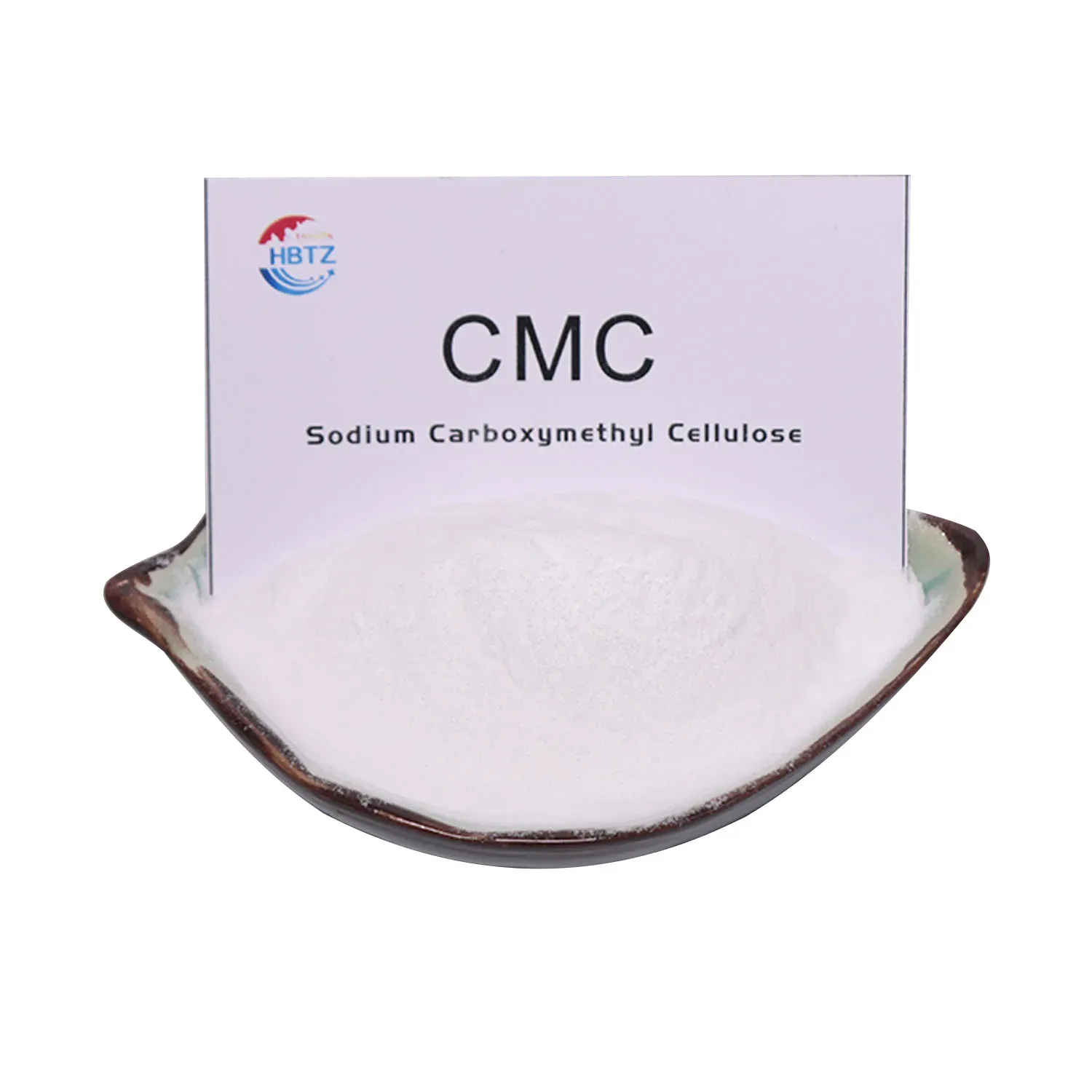
It is a polyanionic compound with good water solubility obtained after chemical modification of natural fibers.
It is easily soluble in cold and hot water.
It has unusual and extremely valuable comprehensive physical and chemical properties such as emulsification dispersibility, solid dispersibility, non-corruption, and physiological harmlessness.
It is a natural polymer derivative with a wide range of uses.
Item |
Range |
Appearance |
White power / Off-white powder |
Chloride(%) |
<1.8% |
Viscosity(1% Solution Mpa.S) |
50-1200 |
Degree of substitution |
0.6-0.9 |
PH |
6.0-8.5 |
Purity |
99.5% |
Moisture(%) |
<10% |
1.Good thickening effect
In surfactant, it has good thickening property.
2.Good water retention
The paste will not dry too fast and crack after application.
3.Emulsion stability
It can improve the favor of the product and prolong the storage time.
High content, easy to process and widely used in a variety of industries
The production process of sodium carboxymethyl cellulose (CMC-Na) mainly includes raw material pretreatment, alkalization, etherification, neutralization, washing, drying and other steps.
1.Raw material pretreatment:
First, the cellulose raw material is washed, dried and cracked. Then, it is hydrolyzed in water at about 100°C for 12 hours, and then boiled with alkali at the same temperature. The concentration of alkali is controlled at 10%-20%, and the boiling time is 3-5 hours. The purpose of this step is to prepare for the subsequent chemical reaction.
2.Alkalization:
Put the treated cellulose into the alkalization kettle, add caustic soda solution, and stir vigorously to alkalize it. The temperature is controlled at 30-40°C, and the alkalization time is 0.5-1 hour.
3.Etherification:
Put the alkalized cellulose into the etherification kettle, add 1.72 times of alcohol and monochloroacetic acid equal to the alcohol, control the reaction temperature at 35°C, and react for 3 hours. This step is the key process for the formation of sodium carboxymethyl cellulose.
4.Neutralization, washing, and drying:
After the reaction is completed, the material is adjusted to be neutral, bleached with 10% sodium hypochlorite, and washed with 75% ethanol to remove the salts produced by the reaction. Finally, it is dried to obtain the finished product sodium carboxymethyl cellulose.
The entire production process requires strict control of temperature, time, and chemical ratios to ensure product quality and safety. In addition, waste liquid and waste residue generated during the production process need to be properly treated to reduce the impact on the environment.
This product is packed in multi-layer paper bags lined with polyethylene layer. Net weight 25KG.
Empty bags can be recycled or incinerated. Unopened packaging can be stored for several years. Open packaging can make the moisture content of this product affected by air humidity. Store in a cool, dry place away from sunlight. Avoid storage under pressure.
For information on product handling, shipping, and storage, see MSDS.