PVA, or Polyvinyl Alcohol, is a versatile polymer known for its unique properties and diverse applications across various industries. Understanding the different types of PVA and their specific uses can provide significant advantages for businesses looking to innovate and optimize their products.
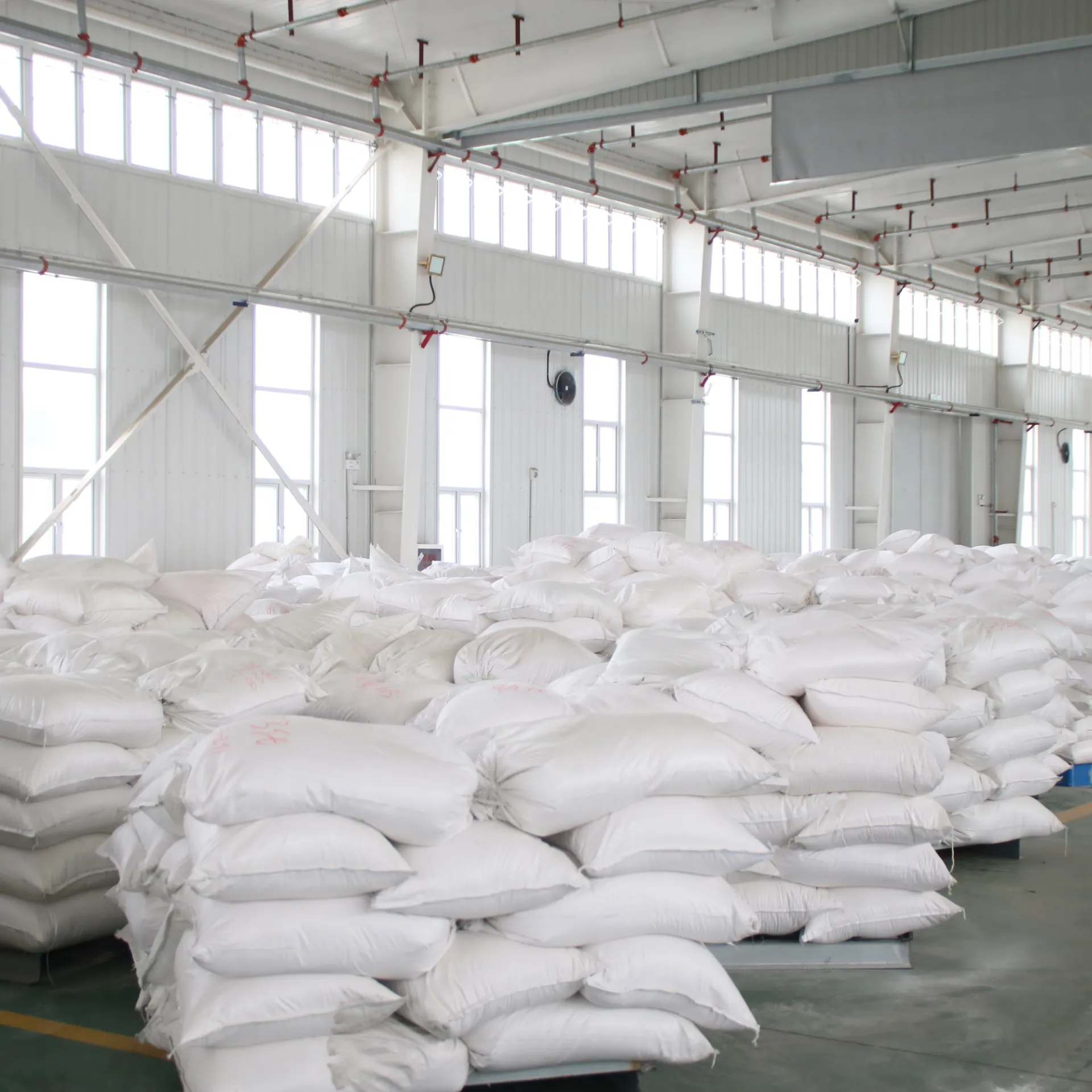
Polyvinyl Alcohol is primarily categorized by its degree of hydrolysis and molecular weight. These factors significantly influence the physical properties and functionalities of PVA, impacting its performance in different applications.
Firstly, PVAs can be classified based on their hydrolysis level into partially hydrolyzed and fully hydrolyzed types.
Partially hydrolyzed PVA typically contains about 87-89% hydrolysis. This variation is known for its remarkable solubility in cold water, making it ideal for applications like water-soluble packaging films, where ease of dissolution is crucial. It offers excellent adhesion properties and flexibility, which are essential in producing adhesives and binding agents across various sectors, including textiles and paper.
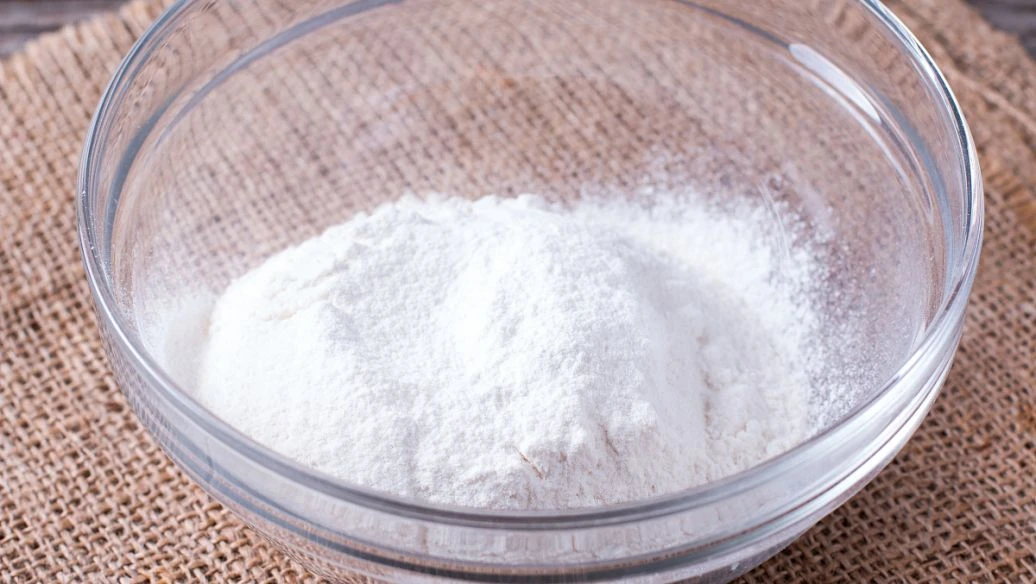
In contrast, fully hydrolyzed PVA, with a hydrolysis level of around 98-99%, exhibits superior water resistance compared to its partially hydrolyzed counterpart. This makes it suitable for applications requiring enhanced durability and low permeability to moisture. Because of its strong film-forming abilities, it finds substantial use in the production of coatings and specialty polymers that demand high tensile strength and durability, such as in the automotive and construction industries.
The molecular weight of PVA also plays a vital role in defining its application scope. Higher molecular weight PVA offers increased viscosity and better film-forming capabilities, beneficial for producing thick films and coatings. On the other hand, lower molecular weight variants offer better solubility and are favored in applications where quick dissolution is needed, such as in the pharmaceutical sector for drug delivery systems.
pva types
One of the most innovative uses of PVA is in the manufacture of biodegradable materials. As environmental concerns continue to rise, the demand for sustainable materials is at an all-time high. PVA’s biodegradable nature makes it an excellent candidate for producing eco-friendly packaging solutions. These solutions not only reduce the environmental impact but also resonate well with the growing consumer demand for sustainable products, enhancing brand credibility and trust.
Furthermore, PVA’s non-toxic and biocompatible characteristics have paved the way for its use in the medical field. It is used in the production of contact lenses and eye drops due to its excellent moisture retention properties. In tissue engineering, PVA-based scaffolds are used to support cell growth and tissue development, showcasing its importance in advanced medical applications.
Another application worth noting is the use of PVA in the electronics industry. Its insulating properties make it perfect for manufacturing resistive components and as a binder in battery electrodes. As technology advances, the need for lightweight and efficient materials in electronics continues to grow, positioning PVA as a material of choice for future innovations.
In conclusion, the different types of PVA offer a wide array of applications due to their unique properties. From packaging and adhesives to medical and electronic applications, PVA’s versatility and adaptability make it a critical component in modern product development. By understanding the specific characteristics of each PVA type, businesses can effectively leverage this material to enhance their products, ensuring they meet market demands and maintain a competitive edge. As industries continue to evolve, the role of PVA in driving sustainable and innovative solutions will undoubtedly become even more pronounced.