The redispersible polymer powder manufacturing process has become a cornerstone in the construction industry, providing essential capabilities to enhance building materials. This intricate process involves transforming liquid polymers into a redispersible powder form, facilitating versatility for various applications. A detailed exploration into this manufacturing process reveals both the complexity and innovation that industry experts have uncompromisingly developed over decades.
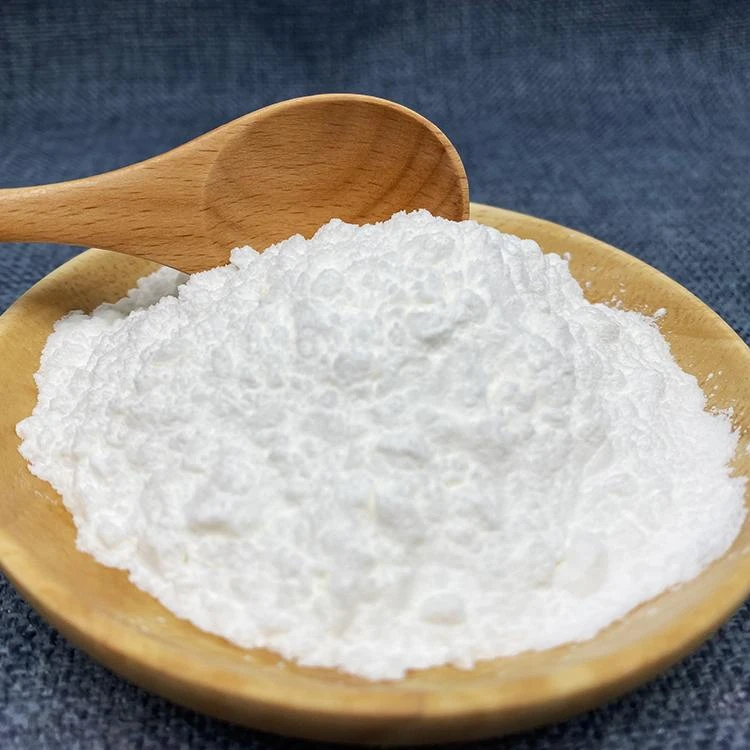
At the heart of the process is the spray-drying technique. This method begins with emulsions, typically made of vinyl acetate-ethylene (VAE) copolymer, vinyl acetate vinyl ester of versatic acid (VeoVa), or acrylic, whose stability and high performance are pivotal. The emulsion is atomized into fine droplets within a hot-air chamber. Here, the water component vaporizes, leaving behind polymer particles that form a powder upon cooling. These powders are then collected through cyclonic separators or bag filters, a testament to the precision engineering involved in maintaining the integrity and consistency of the particles.
Experts in polymer chemistry meticulously design these powders to exhibit specific properties, including controlled particle size, shape, and glass-transition temperature. This customizability ensures that the redispersible polymer powders meet various performance requirements by improving adhesion, flexibility, and water resistance in dry blends. In fact, the expertise applied in tailoring these properties cannot be overstated. The functionality of these powders in end products significantly hinges on the careful selection of base polymers and additives such as anti-caking agents that preserve redispersibility.
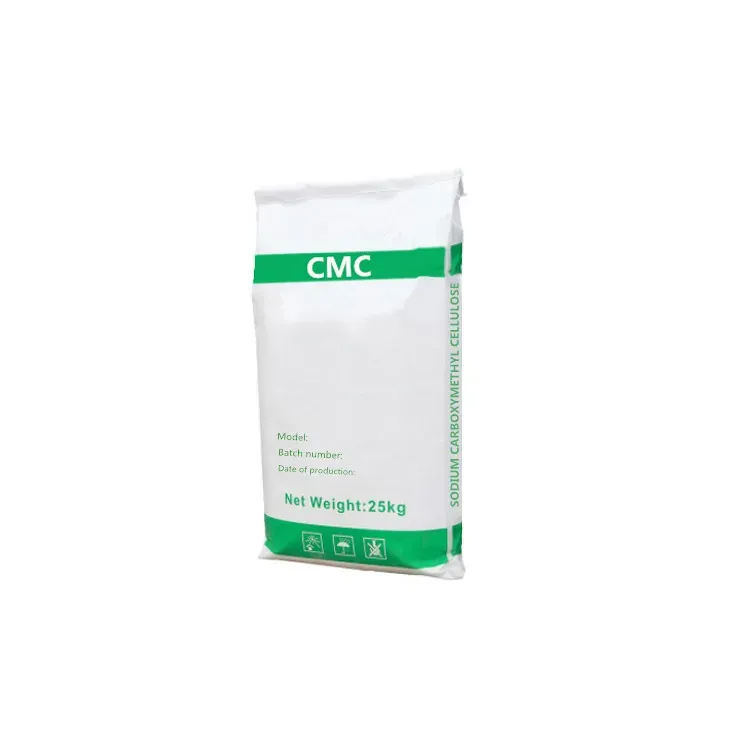
Noteworthy is the emphasis on the eco-friendliness of the process. The reduction of VOC emissions stands as a primary goal, driving the adoption of water-based polymer emulsions. Through innovation, manufacturers like Wacker Chemie AG and BASF have pioneered ways to minimize environmental impact without compromising product quality. Their authoritative research and development efforts highlight a commitment to sustainable practices that also align with evolving regulatory standards.
redispersible polymer powder manufacturing process
Trust in redispersible polymer powders is further solidified by comprehensive industry testing. Rigorous quality control measures, such as infrared spectroscopy and particle-size analysis, ensure each batch adheres to strict specifications. Building professionals rely on these standards to forecast product behavior in diverse conditions, from high humidity to freeze-thaw cycles, underscoring the powders' reliability and performance fidelity.
The process is constantly evolving, with cross-disciplinary expertise from engineering, chemistry, and environmental science driving innovation. Advanced manufacturing facilities harness cutting-edge technology to scale production while maintaining quality. Such continuous advancements illustrate the industry's dedication to meeting the growing demands of modern construction.
In essence, the manufacture of redispersible polymer powders is a sophisticated synergy of science and engineering. Its foundations lie in a profound understanding of polymer behavior and air-drying dynamics, coupled with a steadfast commitment to quality and sustainability. This process not only enhances construction materials but also signifies an ongoing pursuit of excellence in material science, distinguished by expert knowledge and authoritative implementation. For industry professionals and product developers alike, the transparent and well-documented methodologies of redispersible polymer powder production represent a reliable resource for ensuring high-performance construction solutions.