Creating an HPMC (Hydroxypropyl Methylcellulose) gel can be an insightful and rewarding process, particularly for those immersed in the fields of pharmaceuticals, food technology, or cosmetic science. Given its widespread utility—ranging from acting as a gelling agent in food products to serving as a binding and thickening agent in pharmaceuticals—understanding how to craft this gel effectively will be an invaluable asset for both professionals and hobbyists. This guide will delve into the specificities of producing an HPMC gel, underlining aspects crucial for achieving optimal consistency and performance.
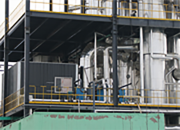
First and foremost, selecting the appropriate grade of HPMC is pivotal. HPMC is available in varying viscosities and properties, often dictated by its molecular weight and degree of substitution. The intended use of the gel will inform the selection process. For instance, in pharmaceutical applications, a high-viscosity grade might be preferable to ensure controlled release or enhanced stability. Conversely, in cosmetic applications where a lighter, smoother gel is desired, a lower-viscosity variant could be ideal.
Once the appropriate HPMC grade is chosen, the preparation begins with hydration—a step that demands both precision and patience. Start with cold water, as HPMC exhibits unique thermal gelation properties, and dispersing it directly in cold water helps to prevent clumping. Gradually sprinkle the HPMC powder into the agitated water. This slow addition is vital because it allows the particles to hydrate evenly without forming agglomerates. After dispersing the powder thoroughly, let the mixture rest and allow the HPMC to swell; this could take several hours, depending on the specific product and its viscosity.
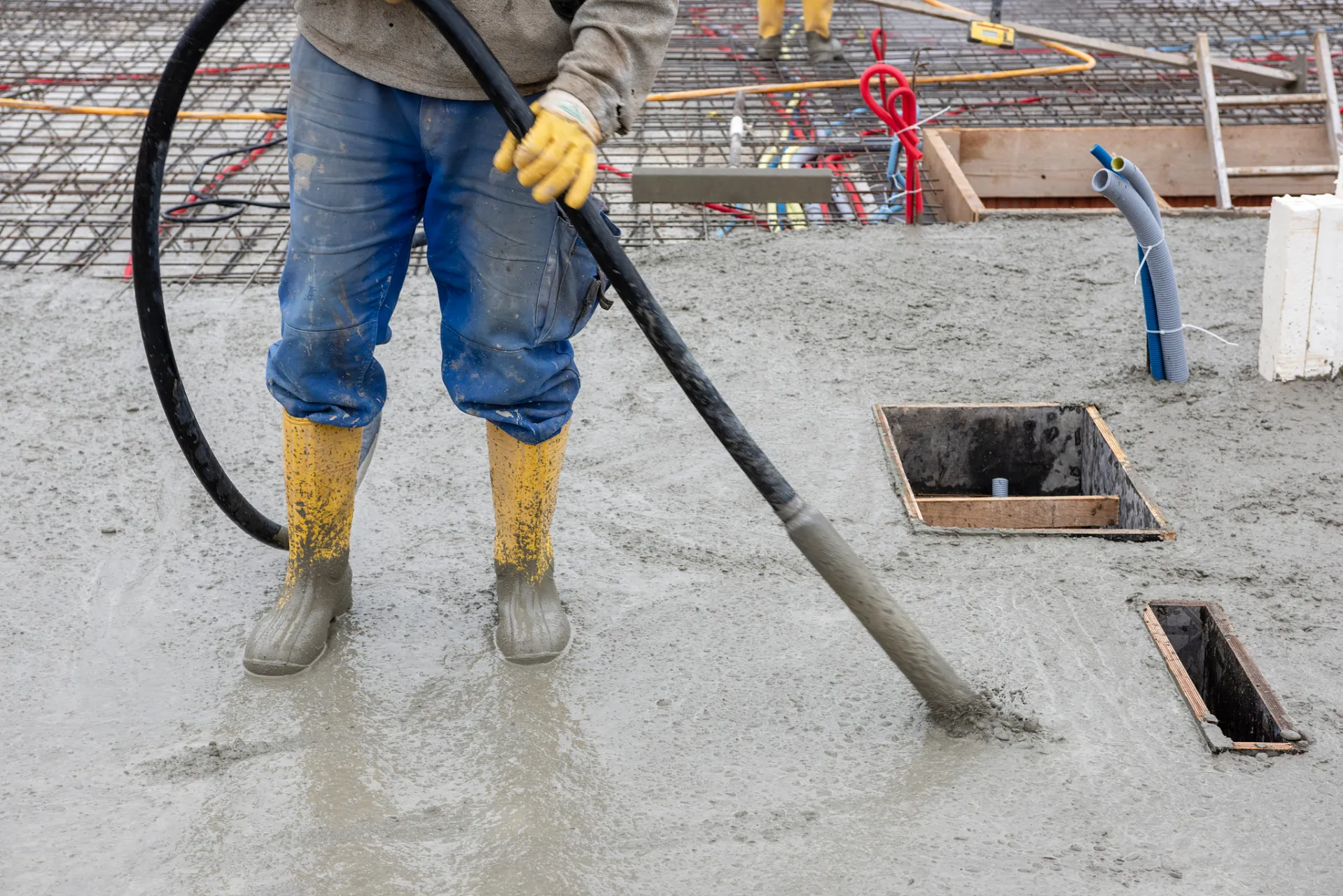
Precision in temperature control during this process cannot be overstressed. The temperature should be carefully increased, ideally to around 60-70°C, while maintaining constant stirring. Around this temperature range, complete dissolution and effective gelation occur, resulting in a clear and uniform gel. Using a water bath to regulate the temperature can offer added control and uniformity, ensuring the gel forms appropriately and retains desired physical properties.
Incorporating additives or active ingredients into the HPMC gel must be approached with caution and expertise. The timing and method of adding ingredients such as preservatives, aromatic compounds, or active drugs—if formulating for pharmaceutical use—are crucial. Typically, these should be introduced after the primary gel has formed to avoid interference with the gelation process. Ensure comprehensive mixing to achieve homogeneity, all while maintaining the desired temperature and continuous agitation.
how to make hpmc gel
Testing the gel for viscosity, pH level, and stability under stress conditions like varying temperatures and mechanical agitation provides objective measures of its performance characteristics. Viscosity tests, for example, offer insights into the gel’s suitability for specific applications, whether it needs to resist flow under pressure or require particular spreading qualities. Conduct stability tests to examine how the gel behaves over time, particularly if it’s meant for product formulations that involve storage.
Understanding the regulatory requirements and safety guidelines associated with HPMC usage in different industries bolsters the authoritative nature of your formulation process. For the food industry, ensure compliance with government-established food safety standards. In contrast, for pharmaceuticals, adhering to Good Manufacturing Practices (GMP) and having robust documentation processes to track the gel’s production and quality checks are essential.
The process of making HPMC gel is as much a science as it is an art. Mastery comes not only from understanding the chemical and physical interactions but also recognizing and respecting the nuances that each application demands. This expertise ensures the creation of products that meet or exceed performance expectations, thereby establishing trust and authority in HPMC gel usage and formulation.
Ultimately, the creation of an HPMC gel is more than just a mechanical process; it's an exercise in applying chemical knowledge, balancing patience and precision, and aligning with industry standards to produce a reliable and versatile end product.