In the expanding universe of pharmaceutical and industrial applications, the synthesis and preparation of Hydroxypropyl Methylcellulose (HPMC) stand as crucial processes. As a non-ionic cellulose ether, HPMC is valued for its exceptional properties as a thickener, emulsifier, and film former. Its versatility makes it an indispensable component in products ranging from adhesives to tablets. A meticulous preparation process ensures these properties are enhanced and preserved.
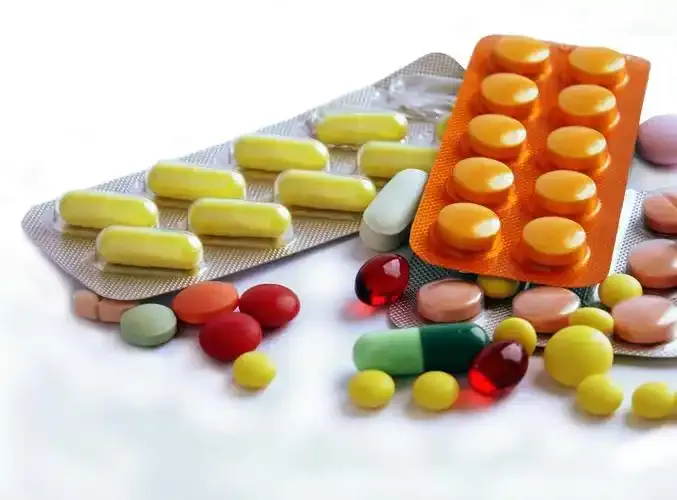
When embarking on the preparation of HPMC, it's essential to consider the specificity of its intended use. This is where the process begins to demand both experience and expertise. The HPMC preparation generally follows a path involving etherification, dehydration, and purification. As a practitioner in this field, the ability to fine-tune parameters such as reaction temperatures, cellulose source, and the concentration of reagents is paramount. The process demands a sophisticated understanding of how these variables interact to yield different grades of HPMC.
To achieve a high-quality end product, starting with a select quality of raw cellulose, usually derived from plant fibers, sets the foundation. The cellulose undergoes a pretreatment stage where impurities are washed away, ensuring that these do not interfere in the subsequent chemical reactions. The core of HPMC preparation is the etherification process, where cellulose reacts with compounds like methyl chloride and propylene oxide under controlled alkaline conditions. This stage is critical, as it defines the degree of substitution – a parameter which ultimately influences the solubility and viscosity of the HPMC.
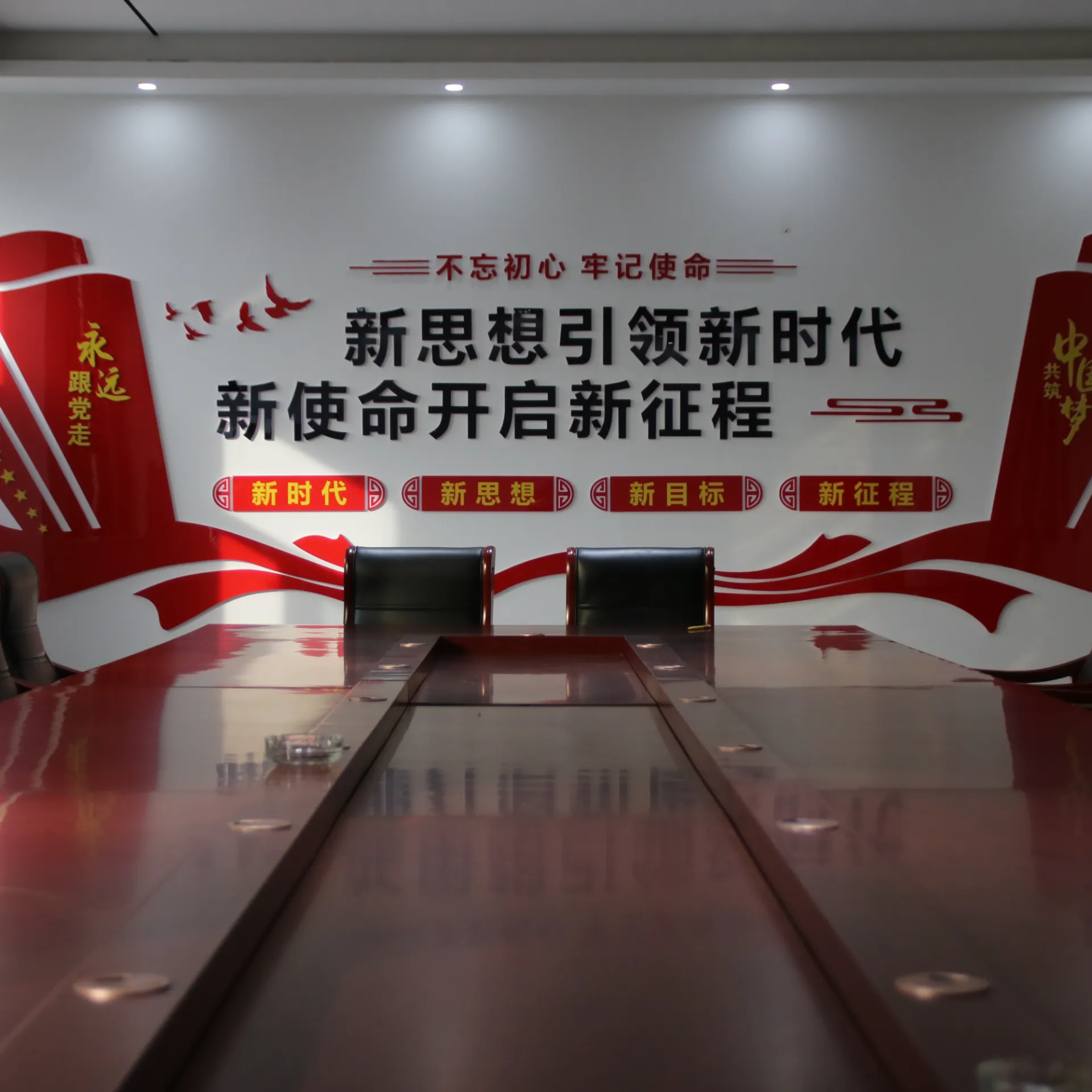
A pivotal aspect of the preparation process is maintaining control over the reaction environment. Measurement precision in both temperature and pressure is critical. Typically, temperatures are kept between 40 to 60 degrees Celsius to promote effective etherification while minimizing thermal degradation. Knowledge of these nuances comes from a combination of hands-on experience and in-depth educational foundations in chemical engineering and materials science.
Upon completion of the reaction, the product is subjected to a series of purification steps. Dehydration removes excess moisture which can affect the powder's stability, while purification rids the blend of residual reagents and by-products. This not only elevates the quality of the HPMC for marketing but also aligns it with safety standards outlined by regulatory bodies such as the FDA.
hpmc preparation
Experience cultivated over time aids in understanding the nuances of differentiating HPMC grades necessary for varied applications. For instance, in the pharmaceutical industry, low-viscosity HPMC is often favored for tablet coatings, enabling smooth application and film formation. On the other hand, high-viscosity grades may be tailored for use in water retention in building materials.
Yet,
preparation does not end with chemical synthesis. Storage plays a critical role in preserving HPMC’s integrity. Proper storage conditions shield the product from environmental factors that could compromise its efficacy. Packaging in moisture-proof, airtight containers, kept in cool, shaded environments, ensures longevity and reliability, underscoring the trustworthiness manufacturers can offer to their consumers.
As we delve deeper into the sustainability trends reshaping industries, the preparation of HPMC also calls for consideration of environmentally friendly practices. Innovators in the field explore biotechnological methods to achieve greener synthesis processes, which minimize waste and reduce the reliance on harsh chemical agents. This not only caters to the eco-conscious consumer but fortifies the ethical stance of brands embracing these practices.
HPMC’s myriad applications have poised it as a product of both economic and functional significance. Its preparation is an art as much as it is a science, calling for the fusion of seasoned expertise and a commitment to ongoing learning and adaptation. By ensuring each stage of preparation is seamlessly executed with precision and care, manufacturers can deliver a high-quality product that meets and exceeds market expectations.