Hydroxypropyl methylcellulose (HPMC), a versatile polymer, plays a pivotal role in the pharmaceutical, construction, and food industries. Understanding its manufacturing process not only highlights the expertise involved but also underscores the authority and trustworthiness of manufacturers who produce quality HPMC.
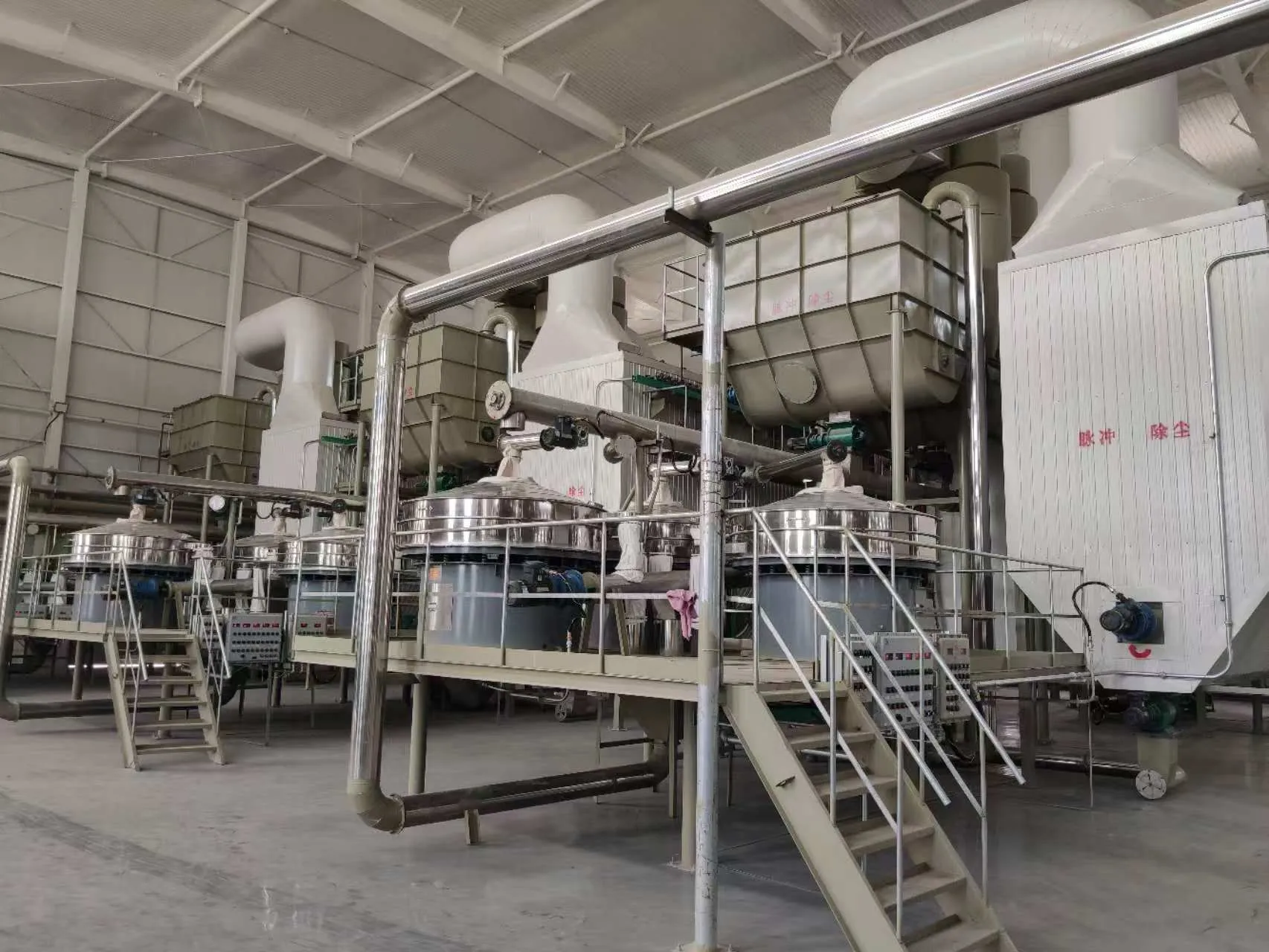
The manufacturing of HPMC begins with the selection of high-quality cellulose, sourced primarily from refined cotton linter and wood pulp. These natural cellulose fibers are an essential raw material, ensuring the end product possesses the requisite purity and stability. The purity of the cellulose forms the basis of the trustworthiness of the final HPMC product, as it influences both its safety and efficacy.
Once the raw material is selected, it undergoes a series of chemical reactions. The first stage involves alkalization, where cellulose is treated with a sodium hydroxide solution. This process facilitates the swelling of cellulose fibers and prepares them for etherification. Expertise is crucial at this stage to control temperature and reaction times, ensuring consistent quality and reducing any possibility of impurities.
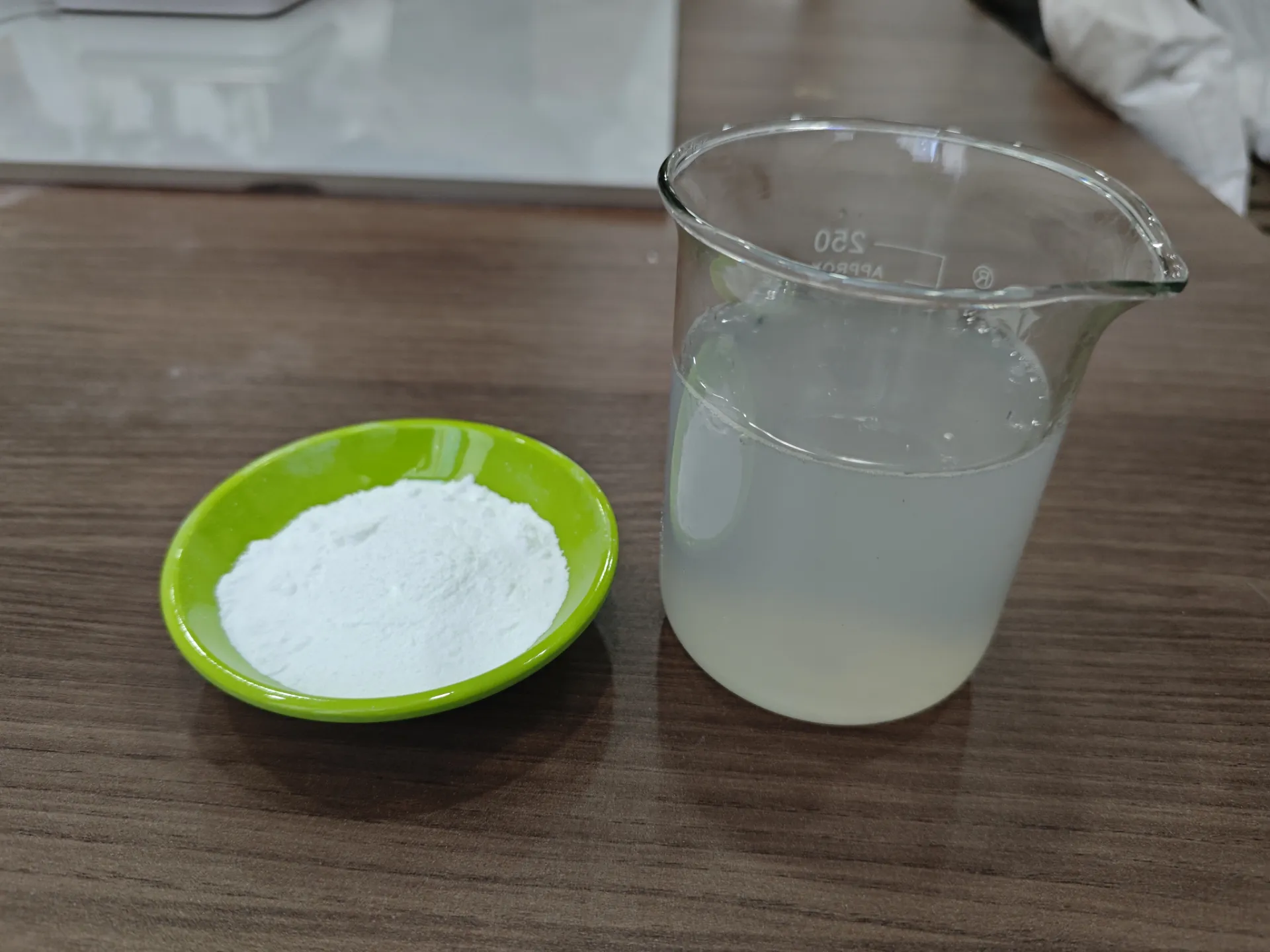
Etherification follows, where the alkalized cellulose is reacted with methyl chloride and propylene oxide. This process introduces methoxy and hydroxypropyl groups to the cellulose backbone. Achieving the correct degree of substitution, where these groups replace some of the hydrogen atoms in the hydroxyl groups of cellulose, is a critical determinant of the physicochemical properties of the HPMC. Authority in the field is reflected by manufacturers who can control this stage meticulously, guaranteeing the desired solubility, viscosity, and thermal stability.
The crude HPMC is then neutralized, typically with an acid such as hydrochloric acid, to eliminate residual alkaline substances. This ensures the product's safety and compatibility with various applications. The subsequent washing step is carried out with hot water, effectively removing salts, by-products, and unreacted raw materials. Expertise in washing and purification ensures the final product meets the stringent requirements of various regulatory standards.
hpmc manufacturing process
Drying is the next step, where the purified HPMC is subjected to specific temperature controls. This process reduces the moisture content to a predetermined level, which is crucial for its storage stability and longevity. At this stage, manufacturers showcase their expertise by utilizing advanced technologies to achieve uniform drying without degrading the HPMC.
Finally, the dried HPMC is milled into a fine powder of consistent particle size, crucial for its performance in applications ranging from pharmaceuticals, where it's used as a binder or drug-release agent, to construction, where it serves as a water-retainer and adhesive. Skilled technicians ensure that the milling process aligns with the high standards expected in each industry, showcasing the manufacturer's authority and commitment to excellence.
Quality control throughout the HPMC manufacturing process is non-negotiable. Each batch undergoes rigorous testing for parameters such as viscosity, degree of substitution, purity, and moisture content. This commitment not only demonstrates expertise but also garners trust from end-users who rely on HPMC for critical applications.
In essence, the HPMC manufacturing process is a meticulous sequence of steps demanding significant expertise and authority. Manufacturers who excel in this realm not only secure a competitive edge but also assure their customers of the product’s reliability and safety, thereby fostering trustworthiness in the industry.